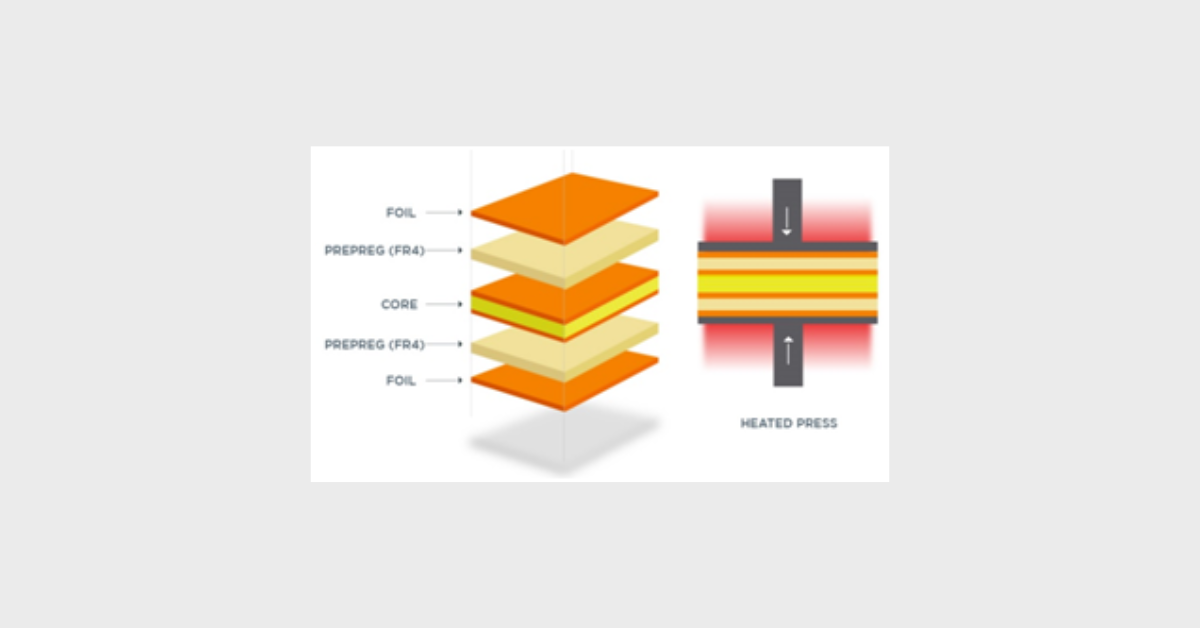
PCB material selection and manufacturing process understanding is important to consider when contemplating a new project. One question is often, the difference between PCB core and prepreg materials. Once the difference between core and prepreg is understood, then what exact materials should be used for your application? What’s the impact on electrical parameters during plating, etching, and curing? As more products for application in GHz frequencies, these points become even more important for properly sizing traces on these materials to avoiding complicated signal integrity problems.
PCB cores are effectively one or more prepreg laminates, pressed, hardened, and cured with heat. The core is plated with copper foil on each side.
Prepreg Core is the isolating material of the PCB. Prepreg acts as a binding substance and as a multifunctional PCB inner conduction material. Prepreg material is impregnated with a resin, where the resin is hardened but not cured. Think of the prepreg as the glue which holds the core materials together. When two cores are stacked on each side of a prepreg laminate, and exposed to heat and pressure, the resin to begin bonding to the adjacent layers. The hardened resin slowly cures through crosslinking, and its resulting material properties start to approach those of the core layers.
The resin material includes a glass weave. The weave can be tight (e.g., 7628 prepreg) or loose (e.g., 1080 prepreg), which is controlled with a loom during manufacturing. Gaps and homogeneity of the glass weave determine the electromagnetic properties (dispersion, losses, and any fiber weave effects seen by signals in the board) of the end product.
FR4 PCB core/prepreg weaves and their important material properties. Source: Isola Group
PCB core and prepreg materials can have different dielectric constants, depending on the resin content, type of resin, and glass weave. This can be a problem when designing boards that require very precise impedance matching as the effective dielectric constant seen by a signal on a track depends on the dielectric constants of the surrounding materials.
Not all prepreg and core materials are compatible with each other, and core/prepreg stacks with very different dielectric constants make it difficult to predict exact dielectric constants and losses.
With any core or prepregs, creepage and leakage current are concern at high voltage. Electromigration of copper and subsequent growth of conductive filaments are one reason for creepage specifications for FR4 materials. This problem, as well as a desire to increase glass transition and decomposition temperatures, have driven use of non-dicyandiamide (non-DICY) resins in FR4 cores and laminates. Phenolic resins provide higher decomposition and glass transition temperatures compared to DICY resins while also providing higher insulation resistance after full curing.
With the obvious structural variations in core and prepreg materials, getting an accurate value for the dielectric constant and loss tangent is important from a signal integrity standpoint. This is especially important when designing for GHz range applications.
The actual dielectric constant measured depends on the test method, routing geometry, specific frequencies (especially in the GHz range), resin content, and even material thickness. The weave pattern in PCB core/prepreg materials makes them highly inhomogeneous and anisotropic, meaning the important material properties vary in space and along different directions. This is the reason we have fiber weave effects, such as skew and fiber cavity resonances. An important parameter that characterizes signal behavior is the effective dielectric constant, which depends on the trace dimensions and layer thickness used in the material selected. Another important parameter to consider is the copper roughness on a given laminate.
When selecting from a range of PCB core vs. prepreg materials, the layer stack manager in design tools can be helpful. They provide access to a materials library that contains important data on a broad range of standardized materials, or you can specify specific material properties for exotic substrate materials. These features increase your productivity while still allowing you to adapt your design to highly specific applications.
For assistance in your material selection please send us your project requirements now, either through our online quote tool, or to orders@optimatech.net. We strive to produce the highest quality PCBs and assemblies to meet all our customer needs.